Crane gantry girders are the unsung heroes of industrial engineering, providing essential support and stability for operations in manufacturing plants, shipping yards, and construction sites. Their role extends beyond merely bearing the weight of massive cranes; they ensure precision and safety in environments where efficiency is paramount. Understanding the nuances of crane gantry girders requires a blend of practical experience and comprehensive technical knowledge.
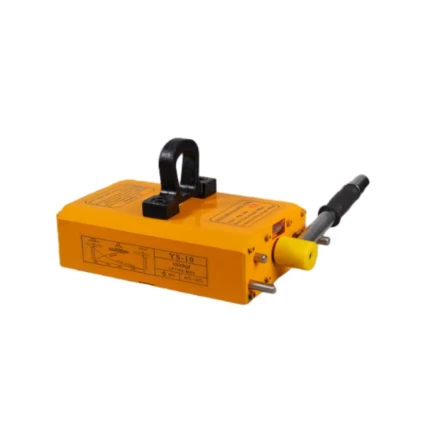
The construction of a crane gantry girder involves meticulous attention to material choice and design specifications. Typically made from structural steel, these girders must be adept at withstanding various stresses, including those induced by heavy loads and dynamic movements of the crane itself. Engineers often select high-grade materials to minimize deformation and prolong the life of the girder. Moreover, the specific type and grade of steel are chosen based on the operating environment—corrosive environments, for example, may require specially treated or coated steel to prevent degradation.
In real-world applications, the dimensions and configuration of crane gantry girders are critical. They are designed to support specific types of cranes, which could range from lightweight jib cranes to mammoth gantry cranes used in shipbuilding. Specific calculations are performed to determine the right span, depth, and thickness of the girder, ensuring that it can handle expected loads without risk of failure. Engineers also take into account factors such as wind load, seismic activity, and additional stresses that might arise during operational peaks.
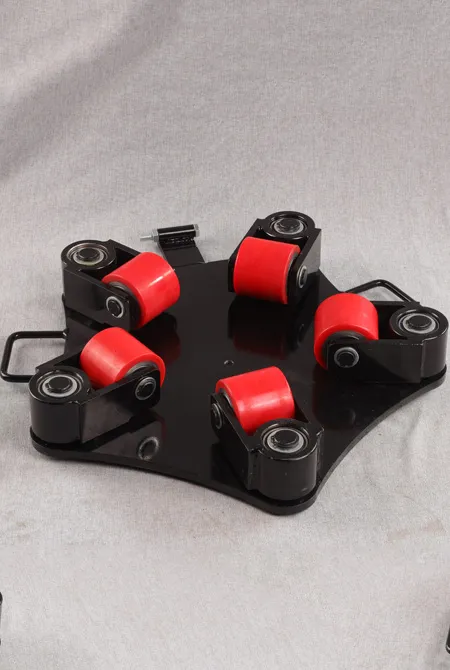
Expertise in fabricating these girders comes from a deep understanding of both theoretical principles and field experience. Installation teams must be adept at handling large, cumbersome steel sections, often in challenging conditions. Precision in alignment and leveling is essential; any discrepancy can lead to operational inefficiencies or even catastrophic failures. Specialist tools and techniques, such as laser leveling and hydraulic lifts, are employed to ensure accuracy during installation.
Authority in the realm of crane gantry girders is often demonstrated by the adherence to international standards and regulations. Bodies such as the American Institute of Steel Construction (AISC) and the European Committee for Standardization (CEN) provide comprehensive guidelines that govern the design and manufacturing process. Compliance with these standards not only ensures safety but also enhances the overall performance and longevity of the gantry systems.
crane gantry girder
Trust is another vital component in the lifecycle of crane gantry girders. Plant managers and engineers have to rely on not only the quality of materials and construction but also on the competence of the teams responsible for their installation and maintenance. This trust is built through rigorous quality assurance processes, regular inspections, and adherence to maintenance schedules. Suppliers and contractors often provide extensive documentation and test reports, which verify the integrity of materials and build quality.
Incorporating advanced technologies into the design and maintenance of crane gantry girders is an emerging trend that enhances their functionality and durability. For instance, the use of sensors and IoT (Internet of Things) technologies can provide real-time data on load pressures and environmental conditions, enabling predictive maintenance.
This proactive approach can significantly reduce downtime and extend the operational life of the girder.
Furthermore, with the push towards sustainability, engineers are exploring the use of recycled materials and energy-efficient processes in the production of crane gantry girders. This not only reduces the carbon footprint but can also result in cost savings over time—benefiting both manufacturers and end-users.
In summary, crane gantry girders represent a complex interplay of engineering discipline, technical proficiency, authority in standardization, and the reliability of skilled implementation. Their importance in industrial applications cannot be overstated, as they form the backbone of efficient and safe operations across numerous sectors. As technology advances, these structures will undoubtedly evolve, integrating smarter materials and designs aimed at meeting the ever-increasing demands of modern industry.