The monorail gantry system has emerged as a pivotal innovation in the field of industrial lifting and transportation solutions. With its unique design and operational efficiency, it has redefined the boundaries of what can be achieved in manufacturing and construction projects. The evolution of the monorail gantry is not just a testament to engineering prowess but a key indicator of its growing importance in the industrial landscape.
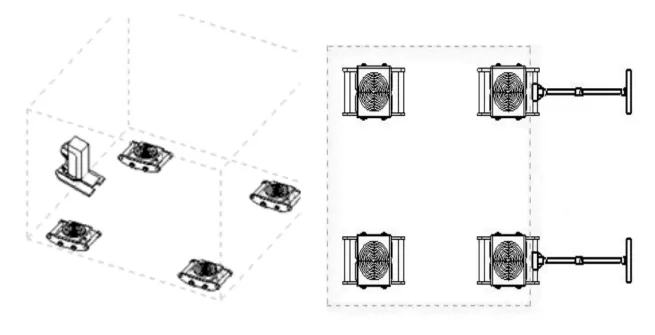
The design of the monorail gantry revolves around simplicity and effectiveness. Unlike traditional gantry cranes, which require extensive setup and large operational footprints, monorail gantries offer a streamlined solution that fits into tighter spaces without compromising on lifting capacity. This adaptability makes them particularly valuable in industries where space is at a premium, such as automotive manufacturing plants and aerospace assembly lines.
What sets the monorail gantry apart is its overhead track system, which allows for a seamless movement of goods across predefined routes within the facility. This track-based system minimizes the need for floor space, eliminating barriers that obstruct personnel or material flow. Such design considerations lead to increased productivity, as handling and transportation become more efficient. Moreover, the ease of installation and modularity mean that these systems can be quickly adapted and scaled as business needs evolve, offering a level of flexibility that further enhances their appeal.
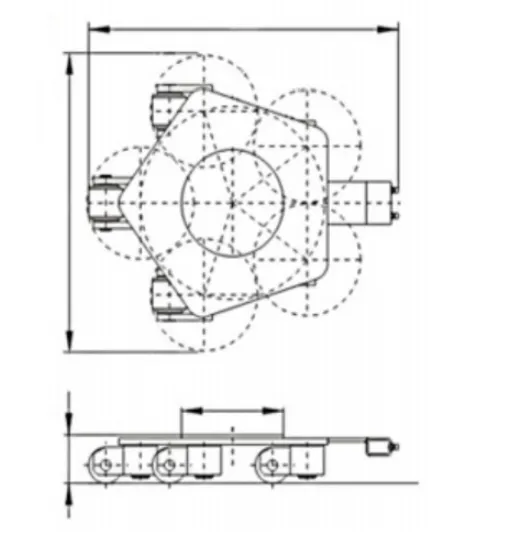
In terms of expertise,
the engineering behind monorail gantries is both specialized and intricate. Engineers and technicians must consider the load dynamics, stress distribution, and potential impact of environmental conditions to ensure safe and reliable operation. The structural components of the gantry are typically fabricated from high-grade steel or aluminum, materials chosen for their strength-to-weight ratios and resistance to fatigue over repetitive cycles. These materials are subjected to rigorous testing to comply with stringent safety standards, which is crucial for maintaining the integrity and longevity of the system in demanding industrial environments.
monorail gantry
Further bolstering its authority, the monorail gantry system integrates with cutting-edge technological advancements. Automation has permeated the sector, with modern systems capable of synchronization with IoT devices and industrial automation platforms. Such integration allows for real-time monitoring and control, significantly reducing the likelihood of human error and ensuring optimal operational performance. Advanced algorithms can predict maintenance needs, thus preventing unexpected downtimes and prolonging machine life.
The trustworthiness of monorail gantries is evidenced by their widespread adoption across multiple industries. Companies that have implemented these systems report enhanced workflow efficiencies and notable reductions in manual handling injuries, a pressing concern in any industrial setting. Testimonials from industry leaders and case studies further consolidate the role of monorail gantries in enhancing operational safety while driving cost savings.
In conclusion, as industries increasingly demand solutions that offer both efficiency and flexibility, the monorail gantry emerges as a compelling choice. Its design sophistication, coupled with the robustness of materials and integration with modern technology, makes it an invaluable asset. The system’s ability to be efficiently implemented and adapted means it will continue to play a critical role. As businesses seek to optimize their operations, the monorail gantry is not just a part of the solution; it is a cornerstone of modern industrial practices, offering a glimpse into the future of seamless material transport.