Machine shifting rollers, a quintessential tool for industries globally, have revolutionized the way heavy machinery and goods are transported within production facilities and warehouses. With an increasing demand in industries such as manufacturing, logistics, and construction, understanding the nuances of these rollers can significantly enhance operational efficiency and safety.
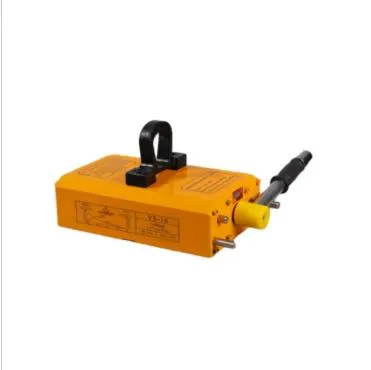
The primary advantage of using machine shifting rollers lies in their ability to facilitate the smooth and efficient movement of heavy equipment. These rollers are designed with high-load capacity and reduced friction in mind, often featuring polyurethane or nylon coatings that ensure minimal floor damage and noise reduction during operation. By choosing machine shifting rollers with appropriate load capacities and material compositions tailored to specific industry needs, businesses can avert costly downtime and equipment damage.
Coupled with their load management properties, machine shifting rollers are instrumental in ensuring workplace safety. The risk of manual handling injuries is dramatically lowered, thanks to these rollers, which allow minimal-force movement of heavy loads. Investing in high-quality rollers that meet industry safety standards ensures that businesses adhere to occupational safety regulations while safeguarding their workforce against handling-related injuries.
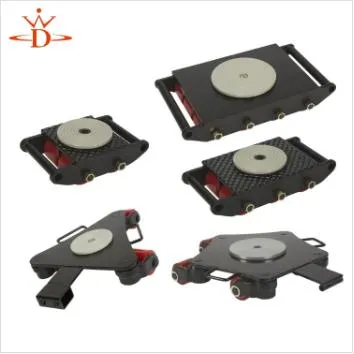
From an operational standpoint, using machine shifting rollers can lead to a marked improvement in the rearrangement speed of heavy machinery, yielding both time savings and increased productivity. In many cases, businesses that adopted these rollers reported a near 50% reduction in the time taken to reposition machinery compared to traditional methods. The reduction in time spent moving machinery correlates directly with increased productive hours,
thereby enhancing overall operational efficiency.
machine shifting roller
Expertise in selecting the ideal machine shifting roller is crucial. Various factors such as load weight, floor type, and frequency of use must be assessed. Expertise extends to understanding the terrain on which the rollers will operate; smoother surfaces may work well with nylon coated rollers, while rougher terrains may require the added durability of steel. Additionally, selecting rollers with added features such as swivel heads or handles can provide enhanced maneuverability, crucial for intricate factory layouts and narrow space operations.
Machine shifting roller suppliers often emphasize the importance of trustworthiness—in both the products they offer and the advice they provide to their clients. Engaging with reputable suppliers who conduct rigorous product testing and offer comprehensive customer support distinguishes the decision-makers who prioritize both performance and product lifespan.
Furthermore, there's a compelling need for businesses to keep abreast of technological advancements in roller design that could enhance performance. Innovations such as self-propelled rollers and those equipped with electronic sensors for monitoring weight distribution reflect the growing trend towards smarter, more automated material handling solutions. These innovations not only provide additional safety features but also offer data insights that can drive more informed decisions around load management.
In conclusion, machine shifting rollers are not merely tools for physical aid; they are pivotal components for strategic planning in material handling and heavy machinery logistics. Businesses seeking to leverage these tools for maximum return must consider the symbiotic relationship between product selection, operational training, and supplier reliability. By doing so, they can drastically reduce costs, enhance safety, and boost productivity, cementing their operations as both efficient and future-ready in an ever-evolving industrial landscape.